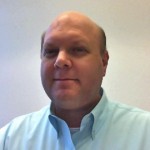
Ian Campbell is the Director of Marketing and New Product Development for the Canadian Welding Bureau (CWB)
The more I work in this industry, the more I realize how much we sell ourselves short. Yes, there have been years of decline in Canada’s manufacturing sector that have put a damper on our industry, but there’s still a huge amount of business available for those who want to work at finding and closing it.
As I’ve mentioned in past columns, welding is a highly transportable skill and right now, in Canada, welding is the trade to be in. It’s a bit of a double win for our industry as welding is not only an in-demand trade, it’s also an industry that cannot be dispensed with, or easily replaced. Simply put wher two pieces of metal come together, you are going to find a welder, or the results of a welder.
Just look at what I call the “BBP” market – that’s buildings, boats and pipelines (and everything that is attached to or “feeds” them). There’s a lot of metal joining going on (or about to go on), but there are simply too few skilled Canadian welders to do the required work.
To be precise, I’m not talking about the number of welders needed, rather the key point I want to make here is the need for “skilled” welders and, by extension, the system we use to define and measure what it means to be skilled.
At a basic level, the word skilled indicates a level of quantifiable training; this can be through a college or university, a trade or unio program, or something more general like Red Seal. All these provide, at a surface level, a standards-based welding curriculum (i.e. based on Red Seal, CWB, ASME, etc.) with the required theory and practical skills training being delivered, as determined by the teaching facility.
In reality, even if these courses follow a standard, they can be unique in content and delivery, leading to inconsistencies in an industry wher there should be none. Course content and delivery issues aside, the measurement of a welder’s skill (and by extension the quality of the course) is determined through practical testing, such as CWB’s Welder Qualification or provincial pressure tickets and it’s here things get interesting.
If you have been following the news, you likely know that welding has become the focus of a lot of attention with respect to pipelines – specifically the issues of weld quality, inspection and engineering oversight. All of which tie back to education and testing. It is also worth noting there are a very small handful of critical welding industries, like pressure vessels, that still handle most welder testing, and administration at a local provincial level.
These are agencies generally working to, and/or interpreting, an industry-adopted guideline or standard on behalf of their industry and/or their provincial government. This system works well when the business end of a welding project (or the welders themselves) stays within one province, but when things go inter-provincial, it brings up some interesting questions. For example, with no nationally focused administration providing oversight, how are the public and industry assured of the consistency of the welds being done as the pipelines wind their way across the country? What if parts of it, or the refineries or ports facilities it’s attached to, are made offshore? Who’s checking up on the foreign welders and fabricators?
If we are to build large projects, which have the potential to greatly impact the people and communities they are built in, it may be wise to do what we did 65 years ago adopt a common testing standard for all welding, secure its use in Canadian codes and laws, and then enforce it uniformly across Canada. But even under such a unified scheme, big projects can only be undertaken if you have the right skilled workers to build them, which brings me back to wher I started – opportunities for Canadian welders.
Over the past year, the CWA has conducted a survey to get a better handle on what an average Canadian looks like – and I’m not talking fashion here. Our goal was to figure out the demographics of Canada’s welding workforce and the findings confirm what, up to this point, has simply been speculation: we have some of the best quality welders in the world, but we need more, and fast.
The average Canadian welder is male, 50 years old or older (49 per cent) or between 31 to 40 (22 per cent), has a college or trade school education (69.9 per cent) and holds a full time salaried/hourly wage job (74.5 per cent). The majority feels that they are paid well (43 per cent), or on par (30 per cent), for the work they do; they have stable employment (63 per cent) and a safe work environment (99 per cent). At face value all this looks good for the future of the trade, however welders in the 18 to 30 age range only account for 19 per cent of those who responded – confirming another issue we felt was true, namely the graying of the trade.
So to wrap things up this month, I will leave you with some thoughts. First, big projects need lots of skilled welders. These welders will need training, and training will need to be delivered and tested consistently across Canada. Second, once trained and tested, skilled Canadian welders will need the freedom to go wher they can help the most, which means their skills are uniformly recognized across the nation. Third, nothing gets done without input, action and leadership. There are many ways to get things started and we would like to hear your thoughts. For starters, why not dro by our Facebook or Twitter pages and leave us your thought on Canada-wide welding standards and testing?
One last thing – if you have not taken our survey, please do so. Your time will help shape an ongoing and accurate picture of welding in Canada.
Ian Campbells column was featured in our November issue.
Follow the CWB on Twitter: @cwbgroupandcwa
Like them on Facebook at: www.facebook.com/pages/CWB-Group-and-CWA
Follow @Cdnmetalworking