Most people walk away from an additive manufacturing demonstration with their jaw hanging lower than when they got there.
Sometimes they’ll fumble with words as they leave, struggling to describe what they just saw. “Science fiction” and “futuristic” are terms that get thrown around a lot. And it’s not hard to see why.
The technology in additive manufacturing is new and fresh, and at the recent International Manufacturing and Technology Show (IMTS) in Chicago it was all some people wanted to talk about.
And rightly so, because building solid parts from powder has plenty of potential. President Obama has even hailed its importance, saying it could signal a renaissance for the manufacturing industry.
But with all the attention lavished on the new kid on the block, there are few who seem to be discussing the potentially awkward relationship that additive manufacturing will have with conventional machining.
The two methods are, in essence, complete opposites.
Additive, as its name would suggest, builds a part from scratch. It takes a computer-generated 3D design, slices it into thin layers called STL files, then melts powder with lasers, ‘printing’ the layers by fusing them together. Plastic powder is commonly used, but metal-based products are becoming more prevalent.
Of course, traditional machining does the exact opposite. It removes chips from a larger block of material, shaping it into a functional part with cutting tools – whether it’s as big and complex as jet engine blades or as simple as a small flange.
So how could these two methods possibly co-exist?
David Bozich, a business manager of Machine Tool and AMPD (Additive Manufacturing Products Division) with Renishaw, has spent lots of time with traditional manufacturing, and now working firsthand with additive, he takes a diplomatic approach to how these two processes complement each other.
“You’ll find the impact that additive has on conventional machining is going to (create) very little competition. You’re going to find that one technology will augment the other,” Bozich says.
“For example, you build a part with additive capabilities, but you might have to then take it out and use conventional machining to do something else – drill and tap holes, or maybe do a fly-cut.”
This scenario would seem to make sense, because for all the advantages of additive manufacturing there is still a nagging drawback – speed.
In a head-to-head race, additive doesn’t even come close.
“But the thing is, there are parts that lend themselves to additive that you just flat-out can’t do with conventional machining. The lattice structures? You’re just not going to be able to produce those with conventional machining.”
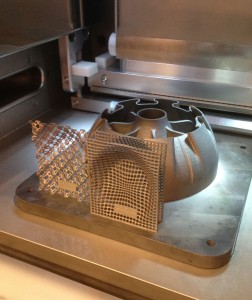
Lattice structures are well suited to additive manufacturing.
These structures are a great example of the potential that additive manufacturing brings. The additive process easily produces a lattice (or honeycomb) structure inside, giving it strength like a solid part while shedding massive amounts weight – a revolution that could do wonders for industries like aerospace or automotive.
But, for all of its advantages, there is indeed another drawback raw materials.
For all its advanced technology, additive can’t use many common (or desirable) materials.
“We’re in development of titanium, tungsten carbide, tungsten, some silicones, [material] like that. But, that’s one of the constraints,” says Tom Pasterik, a designer with ExOne, a company that specializes in additive manufacturing.
Pasterik believes the two methods can live in harmony, but envisions a time when additive takes a bigger share of the marketplace and becomes more widely used.
“Additive and traditional will always co-exist with each other. They might flip-flop… I would love for it to!”
So for now, additive’s challenge to the old guard is mostly limited by time and materials. But even when additive manufacturing becomes more refined, it seems it could happily exist alongside machine tools. The only question left, is just what share of the workload each will take on.