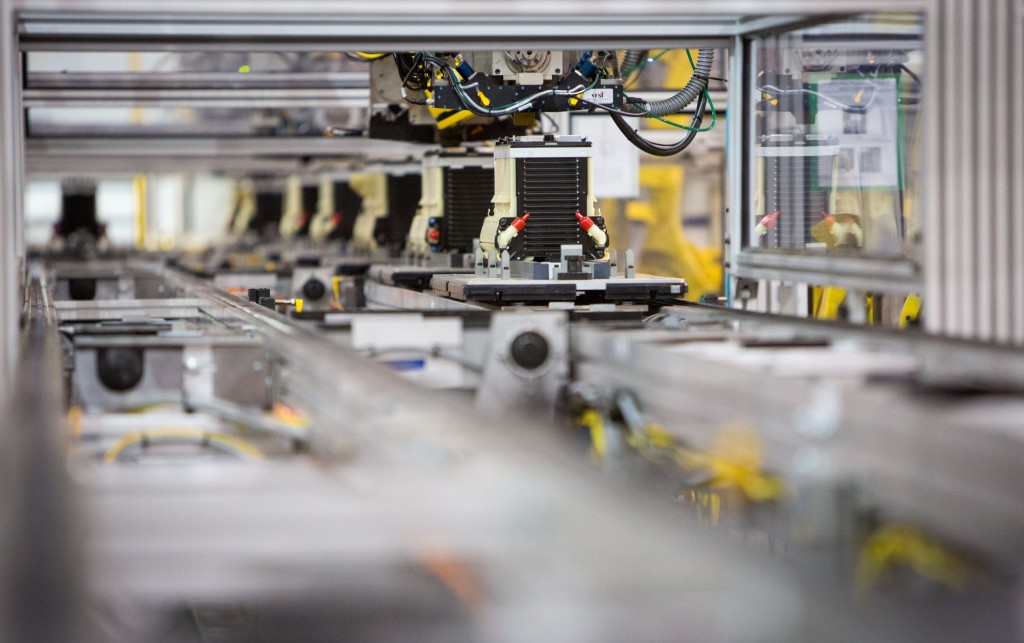
General Motors ultrasonic welding process, used for batteries in the new Cadillac ELR. (Photo: GM)
DETROIT – General Motors (GM) is using an ultrasonic welding process to produce batteries for their new Cadillac ELR, an extended-range luxury car that will go on sale in early 2014.
The welding technique, which is more common in aerospace and medical industries, will be used to join metal electrode tabs on the ELR’s 16.5-kWh lithium-ion battery system.
Ultrasonic welding is advantageous because its performance and quality is very predictable from one task to the next.
Each ELR battery has close to 200 ultrasonic welds, which Cadillac believes improves the quality enough to offer an eight-year, 100,000-mile battery system warranty.
“Ultrasonic welding is a far superior joining technology in applications wher it can be deployed,” said Jay Baron, president and CEO of the Center for Automotive Research in Ann Arbor, Mich.
“Cadillac’s innovative process will produce batteries with superior quality compared with traditional methods – and do it more efficiently. This is one example of technology development that is becoming pervasive in today’s world class vehicles.”
RELATED: Automaker to build new Cadillac XTS in Oshawa
Short cycle times, low capital costs, and manufacturing flexibility through the use of automation are other advantages of ultrasonic welding.
Ultrasonic welding uses specialized tools called an anvil and horn to apply rapid mechanical vibrations to the battery’s copper and aluminum electrodes. This creates heat through friction, resulting in a weld that does not require melting-point temperatures or joining material such as adhesives, soldering or fasteners.
An integrated camera vision system is used to shoot a reference image of the weld area prior to the operation to achieve pinpoint accuracy.
Quality operators check electrode tabs before and after welding, and the system monitors dozens of signal processing features during each weld.
The battery-specific welding process is a result of collaboration among General Motors’ Manufacturing Systems Research Lab and Advanced Propulsion Center, and the Brownstown plant.
GM first applied the process on the Chevrolet Volt, and further refined it for ELR.
“This effort is an outstanding example of teamwork between research and manufacturing engineering,” said Catherine Clegg, GM vice president of Global Manufacturing Engineering.
“It has helped integrate the use of highly technical, complex technology into a sustainable manufacturing process, which means we can consistently deliver high-quality batteries to our customers for the Cadillac ELR.”
The 1.6 m (5.5-foot) long, 198 kg (435lb) pack supplies energy to the electric drive unit capable of 295 lb-ft of instant torque (400 Nm) to propel the vehicle.
Using only the energy stored in the battery, the company estimates the ELR will deliver a range of about 56 km of pure electric driving.
Depending on the temperature a complete recharge can be achieved in about 4.5 hours using a 240V outlet.
The Cadillac ELR is built at GM’s Detroit-Hamtramck Assembly Plant. The battery pack is built at Brownstown and shipped to Detroit-Hamtramck for assembly.