Delcam presents the latest developments in the company’s PowerMILL CAM system for high-speed and five-axis machining. The company introduced the features at its annual updat meeting in Windsor last month.
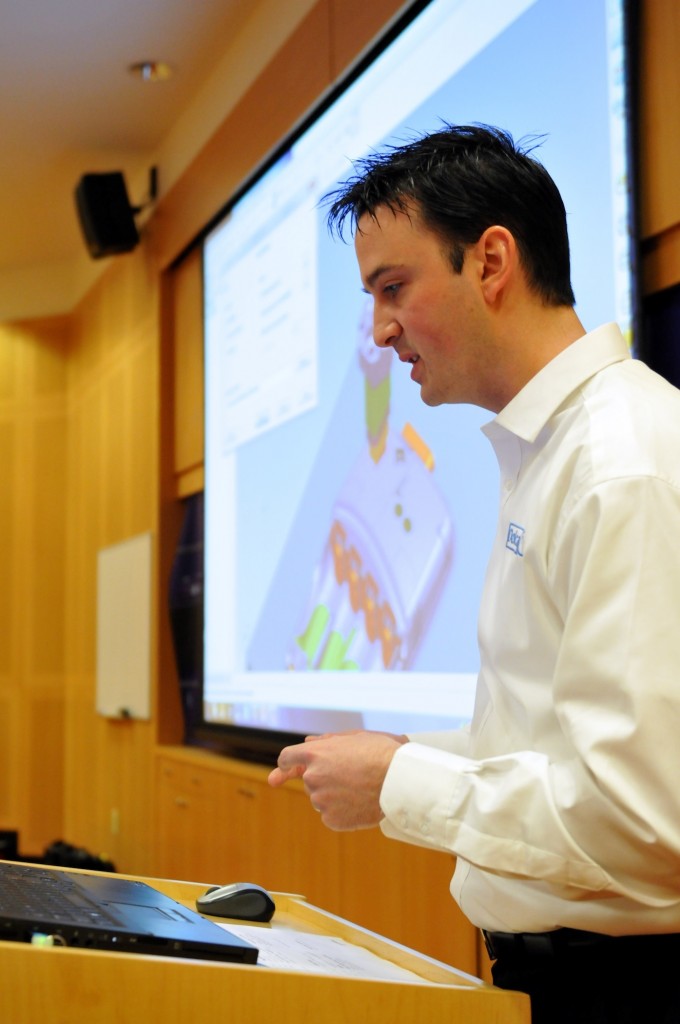
Delcam’s Craig Burney presented the latest developments in PowerMILL at the Windsor User Meeting
At the event, Craig Burney, Application Engineer based in the Delcam Windsor office, presented the 2015 release of PowerMILL. This includes improvements to the Vortex high-efficiency area-clearance strategy, expanded collision checking to also cover near misses, and more efficient raster finishing.
Vortex produces safe toolpaths with a much deeper cut by using a controlled engagement angle that maintains the optimum cutting conditions for the whole toolpath. As a result, higher feed rates and material-removal rates are possible, making the cutting time shorter by as much as 70 per cent. In addition, cutting is undertaken at a more consistent volume-removal rate and at a near constant feedrate, so extending tool life and protecting the machine.
Mr. Burney also previewed a new rib-machining module and other functionality planned for the PowerMILL 2015 R2 release.
Reinforcing ribs are required in many types of plastic mouldings, from electrical housings to containers to furniture. They are typically much deeper than they are wide, which poses special challenges when machining the cavities needed to form them. In many cases, these challenges prompt companies to use EDM to form the features rather than machining. The new PowerMILL module makes it much easier and safer to program the machining of cavities for narrow ribs, even when the cutter’s length is much greater than its diameter. Using the dedicated rib-machining strategy gives a better surface finish than using a standard finish-machining option and also improves efficiency by limiting the number of air moves.
The first stage of the process is to create a pattern for a single rib, by sketching a line along its length. PowerMILL uses this line to identify automatically all the surfaces needed to form the rib. The machining sequence is then calculated. Usually, the machining will either be undertaken by cutting progressively deeper along the centreline of the cavity using a form tool matching the rib profile or by profiling along either side of the rib with a standard tool.
In many cases, most, if not all, of the ribs in a part will have similar depth and width profiles. Thus, once the user is happy with the sequence developed for the first rib, the same machining strategies with the same tooling can be applied across the complete network of ribs, minimizing programming times.
For more information, visit www.delcam.com.