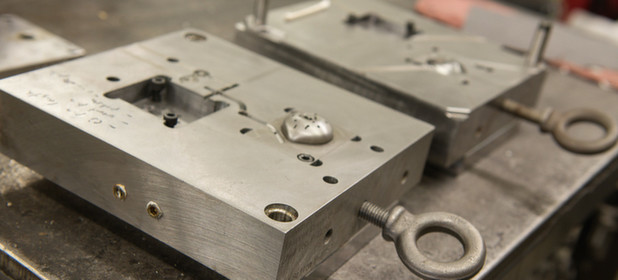
US-based Ash Industries is taking advantage of recent advancements in CAM software to dramatically streamline its processes for making the tools used for moulding medical parts. Some CNC programs are delivered to the shop floor within 15 minutes. By Lynn Gorman.
Ash Industries can deliver the first CNC programs for cutting mould plates to the shop floor in as little as 15 minutes after the completion of the mould design. In some cases, the advanced cutting strategies incorporated in these programs make it possible to mill all of the mould plates within one day.
Euromold presents itself as a strong and future-oriented show
Super-Mold parts thanks to manufacturing efficiency
These improved manufacturing efficiencies are the basis for the company's Super-Mold Program that offers a production quality mould (guaranteed for life) and 1000 moulded parts for a set price. Super-Mold parts are available within three different size envelopes and pricing varies accordingly.
According to Ash Industries' president Hartie Spence, the ability to get moulded parts so quickly and inexpensively is making medical device manufacturers think twice about using intermediary processes like stereo lithography and 3D printing for prototyping. The big advantage of this approach is that the medical device company can have a production mould ready to go as soon as necessary approvals have been obtained.
He said that improved manufacturing efficiencies that allow his company to offer such competitive pricing and fast turnarounds derive from a very skilled and focused manufacturing staff in combination with advanced features that began to appear in its CAM software (Mastercam from CNC Software) starting around 2009.
In 1990 Hartie Spence was an electrical engineer working in the aerospace industry. His independent nature and lifelong passion for making things drove him to move back to his home in Louisiana and start a manufacturing business. He acquired the license to make a patented injection moulded product that did not succeed commercially. After this failed initial venture, his primary remaining assets were some manufacturing space and an injection moulding press. He decided he would take a shot at becoming a custom moulder.
By his own admission, Spence knew almost nothing about moulding or mouldmaking, but he did have a command of critical thinking and manufacturing processes. This allowed him to figure out how to meet the needs of a succession of customers. Spence estimates that his company is now working on the 20th generation of referrals from those first satisfied users. During the intervening years the company has grown through good times in bad, to the point wher 50 people are employed making and delivering parts from a variety of processes that include injection moulding, silicone moulding, roto-moulding and metal injection moulding. Fourteen machines are used in these processes. about 70% of this work is for medical device manufacturers.
Spence initially purchased moulds from local tool & die shops, but he became frustrated because they could not consistently deliver what he envisioned. Subsequently, in 1996 he acquired a band saw, a surface grinder, and 3-axis CNC mill with a rudimentary version of Mastercam for programming it and began making his own moulds. "It’s a joke around here," he said. "I made some really bad tools and there are people here who won't let me forget it. Part of the problem was using a very basic level of software that required several hours of work to generate a simple program."
He got past his initial struggles programming his CNC equipment by consulting with MLC CAD, his local Mastercam dealer. They fortified him with versions of the software that were much more efficient for his needs and have served as manufacturing process consultants to the company through numerous updates to the software. Spence said what really turned his toolmaking operations around was when he turned the programming over to Eddie Higginbotham, a manufacturing engineer who programs all of the CNC mills and organizes workflow through the shop. Today the company has four 3-axis CNC machines, two plunger EDMs, and a 7-axis Swiss lathe.
Standardised processes reduce costs, improve productivity
Most of the Super-Mold tools are MUD (Master Unit Die) moulds consisting of six or seven modular plates that slide easily into a standard frame. This approach both reduces the overall cost of tooling and allows for fast tool changes at the moulding machine in keeping with just-in-time manufacturing. The MUD concept also makes it easy to modify individual plates rather than complete tools during the mould development process. During the past eight years Higginbotham has developed standardised processes for making MUD tooling that has dramatically improved his programming productivity along with that of company's CNC equipment. He said, "The last three years have shown the most dramatic improvements based on the new toolpaths and the dynamic toolpath training I received from MLC CAD."
When Higginbotham first started doing all of the CNC programming, he would start from scratch with each electrode or mould plate that came his way. He soon noticed that the many of parts that came in for CNC programming had common elements. Soon he was setting up programming templates within Mastercam so that whenever possible repetitive tasks were done automatically, with feeds and speeds already established and optimised within the template.
He said, "With the advances Mastercam has made in the last three or four iterations, our productivity in the shop has skyrocketed. I am programming faster. I have templates set up for each of the mould plates and a template for the electrodes. I merge my geometry from SolidWorks into Mastercam -- I'm picking lines, picking surfaces, right from my default file and programming faster than I ever thought possible. Electrodes that used to take me a half an hour or so, I am now programming in minutes."
Higginbotham said that programming toolpaths to cut the geometry indicated in the CNC program is almost instantaneous because he now relies on just a small number of material-aware toolpaths that will handle just about anything he needs. "I used to spend a lot of time figuring out what toolpath I was going to use to get at different areas of a cavity. Now Mastercam has these new dynamic toolpaths nailed down so well, I know the software will figure it out. I just pick the surfaces and set containment boundaries and let it go. It is actually fun."
Dynamic toolpaths do not cut blindly but are "aware" of the condition of the material during every stage of machining. They use this intelligence to automatically adjust feeds and speeds to avoid burying the tool. Cutting is done at high speeds at shallow radial cuts using as much of the tool’s flute length as possible. This approach minimises tool wear and stresses on the part and reduces cycle times. "Cutting-wise, we have taken as much as 70% off of some of our cycle times. For example, electrodes that used to take five minutes are coming off the machine in 30 seconds."