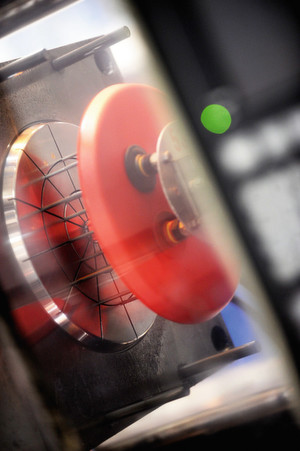
A leading UK injection moulding shop for the engineering and industrial sectors uses Visi software for more than mould tools. The company designed and produced a secondary operation jig that halved the manpower required for shop-floor assembly.
Some software for designing moulds can be used in other processes, according to Carl Martin, the technical manager at Rutland Plastics in Oakham, UK. He noted that the Visi system from Vero is not just a CAD/CAM system for creating injection moulding tools, it is a powerful system for anything in the design world.
A single program covers the gamut for design
Martin noted that the software’s role in ensuring the company could competitively produce a pipe coupling for the drainage industry is an example of its versatility. The shop used the software to create a 3D-printed prototype, the mould tool for production, and a jig to automate a manual part of the operation.
German machine tool orders up by 7%
Carl Martin says the mesh functionality within VISI was a useful tool when preparing the model geometry for printing on its Objet Connex 350 3D printer. The mesh feature set provides tools to clean-up problematic vertices, simplify, fill holes and analyse the mesh topology. Printing a fit-for-purpose prototype meant the customer could fit the physical model to the pipes so it functioned as expected before building the mould tool. “It’s expensive to change tooling if the moulded part isn’t correct.”
As the part had already been designed, it was a seamless CAD through CAM process to make the mould in P20 hardened tool steel. The software’s model preparation tools inspect data for moulding feasibility, while draft analysis checks the model to identify potential design issues. “We used the split line and plane creation function for the two cavities, and then built up the ancillaries around that to design the tool as a whole” This reportedly ensured the accuracy of each aspect: cavity plates, the backing plate, the ejector system, the risers and the clamping plates.
Another important aspect was how the software’s injection simulation showed optimum moulding conditions by identifying the ideal locating gate positions. “It was vital for us to verify wher the part needed to be gated, which areas may be difficult to fill, and wher venting needed to be placed into the tool.” The software showed the company how the tool would perform on the moulding machine.
The High Density Polyethylene (HDPE) component links two pieces of pipe by electrofusion, using special fittings that have built-in electric heating elements that are used to weld the joint together. In order to be successfully welded in the field, brass continuity pins have to be inserted before the part is shipped out of the factory. “Originally we had one operator managing the turning and wire laying, with a second person manually inserting the pins which hold the wire in place.” Automating the pinning process and reducing manpower from two to one is said to have been essential for the shop to remain competitive.
“We used Visi to design the jig to handle this job, from the ground up,” Martin explained. “VISI created the components and animated all movements showing how it would function on the shop floor.”