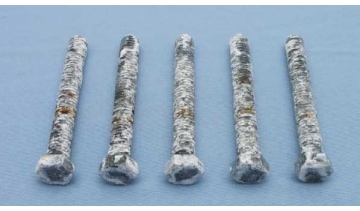
Zinc Plating/Trivalent - 72 hours of salt spray testing. Image at top left, ZnCoat after 240 of salt spray testing.
NOF metal Coatings North America Inc. and Curtis metal Finishing Co. have launched ZnCoat, a new finish that offers effective solutions for the problems that have been encountered by users of zinc plating for fasteners and small parts.
ZnCoat, a zinc-rich coating for ferrous metals, offers several advantages for high strength fasteners when compared to electroplated zinc. The finish is chromium-free (no hexavalent or trivalent chromium), and provides superior corrosion resistance with a thin film, without risk of hydrogen embrittlement, claims NOF metal Coatings.
Most importantly, these features and more are available at no extra cost when compared to zinc plating, baked for hydrogen embrittlement relief. ZnCoat is applicable for industries such as agriculture, construction, appliance, recreation and marine, providing these markets with a higher performance alternative to conventional zinc plated finishes.
The zinc in the ZnCoat is passivated without the use of toxic materials. ZnCoat is free of chromium, nickel, cadmium, lead, barium and mercury and meets RoHS, REACH & WEEE environmental regulations. By comparison, conventional zinc plating is passivated by the use of hexavalent or trivalent chromates. Chromates provide a thin-film passivation layer, but only on the surface of the zinc plating. Subsequently, during installation or in-use, this fragile film may be damaged and lead to premature zinc oxidation.
The new finish offers a solution to this problem: environmentally friendly passivation agents and corrosion inhibitors are found throughout the film, and so the coating is far less susceptible to early failure. Furthermore, the unique corrosion inhibitors found in ZnCoat allow for continuous release throughout the life of the coating.
It provides sacrificial protection as the zinc corrodes to protect the steel substrate. The coating is further enhanced by a self-repairing mechanism. If a coated fastener is abraded during installation, zinc oxides and carbonates form at a controlled rate at the damaged area, sealing the breach in the coating, and thus restoring barrier protection. Compared to conventional zinc plating, ZnCoat consistently achieves over 240 hours of ASTM-B117 salt spray corrosion protection, as well as higher cyclical corrosion performance and real-world outdoor weathering resistance.
The finish is applied to steel parts through a non-electrolytic dip spin coating process. In contrast, the process of zinc electroplating produces hydrogen as a byproduct. Some of this hydrogen can be trapped beneath the plated layer and cannot escape. For hardened parts, this can cause hydrogen embrittlement of the steel substrate, leading to delayed fracture of the part after installation. For this reason, high hardness parts must be baked to relieve the entrapped hydrogen, but this step adds cost, and does not guarantee the part is free from embrittlement. The ZnCoat process is free from the risk of hydrogen embrittlement, thus reducing a processing step for high hardness fasteners.
For threaded fastener applications, ZnCoat has a tight, consistent friction coefficient (CoF). Lower CoF can be achieved with conventional wax-type topcoats, as is common with electroplated fasteners. The finish is compatible with microencapsulated, anaerobic and nylon type thread adhesive and sealant patches. Because the dry film is thin (8-10 microns / 0.3 – 0.4 mils), no adjustments to thread tolerances are necessary.
ZnCoat provides excellent UV protection for outdoor applications. The coating performs to greater than 2,000 hours with no change in appearance in Q-Panel ultraviolet (QUV) testing (UVB at 158o F / 70o C). Fluorescent UV lamps simulate the damaging effects of sunlight. In a few days or weeks, the QUV test can produce damage that would occur over months or years of outdoor exposure. It resists fading, chalking, cracking, crazing, hazing, blistering, gloss loss, strength loss and embrittlement.
It’s applied under license by Curtis metal Finishing, which took the lead in bringing ZnCoat to market.
NOF metal Coatings North America